✔ Wide range of applications for processes: from soldering and laser engraving to welding.
✔ Availability of models of units with different built-in fans in noise-absorbing casings – the ability to choose a filter of the required performance, which is optimal for the required models of exhaust devices and, accordingly, the tasks to be solved.
✔ The ability to select the required amount and combination of filtration stages allows you to take into account the specifics of technological processes, ensure high cleaning efficiency, and also increase the service life of filter cartridges.
✔ Availability of models with a configuration of up to 4 stages, combining the following types of filtration.
· pre-filter ME-INL / PF made of stainless steel (filter class G3) – washable.
· Filter cartridge MK-004 (filter class F9) – the main filter.
· Filter cartridge HFME-3-25 (filter class H13) – additional high-efficiency HEPA filter.
· Carbon filter cartridge DinCarb V M5 (filter class M5) – neutralization of odors, solvent vapors, nitrogen vapors, ozone, and some other toxic gases.
✔ Convenient control over filter clogging due to built-in differential pressure gauges at each stage of cleaning (except for the carbon cartridge, which is recommended to be changed together with the main cartridge MK-004, but at least once every six months in a one-shift operation mode)
✔ Increased service life of replaceable filters due to increased filter surface area.
✔ Simple installation and maintenance that do not require special training.
✔ Low cost of units and replaceable filter elements.
The filter unit is prefabricated metal, consisting of:
• a receiving chamber, the inlet openings of which have fasteners for connecting various models of lifting-and-rotating extraction arms of BEA and BEA-200 series by SovPlym.
• a vertical block of chambers with filter elements installed in them, which are responsible for a certain stage of cleaning;
• module with an exhaust fan (only for models with a fan);
• brackets on the back of the casing for installing the unit on a vertical surface.

Unit design using the example of the DCA-W-42 model (without built-in fan)
1 – receiving chamber;
2 – main cleaning chamber;
3 – high-efficiency cleaning chamber (only for models MF-H-32, MF-H-42)
4 – differential manometer;
5 – carbon filter chamber (only for models MF-H-41, MF-H-42);
6 – transporting eye hook; |
7 – flange for connecting the air duct;
8 – chamber door;
9 – pre-filter;
10 – filter cartridge MK-004;
11 – filter cartridge HFME-3-25;
12 – carbon filter cartridge DinCarb V M5;
13 – mounting bracket |
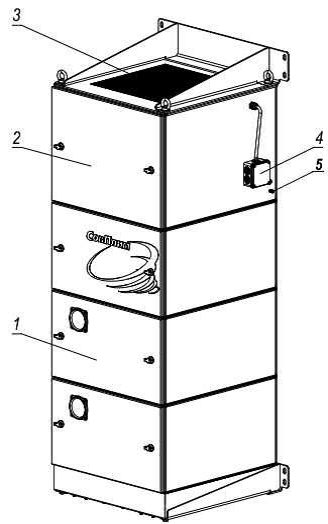 |
1 – filter module;
2 – fan module;
3 – top sheet;
4 – terminal box;
5 – grounding screwFilter models with a built-in fan (for example, MF-H-42-F4) |
Principle of operation
The first filtration stage separates the largest dust particles. This occurs in the receiving chamber due to the expansion of the flow and a decrease in its speed.
Then, the remaining large and medium particles are retained in the ME-INL / PF pre-filter (filtration class G3).
Small particles up to 0.4 microns in size with an efficiency of ≥95% are retained by the main fine filter MK-004 (filtration class F9).
The remaining smallest particles ≤0.3 μm are captured by the HEPA filter HFME-3-25 (filtration class H13). Models with a HEPA filter are recommended for use in cases where the purified air will be returned to the room.
Further, toxic gas constituents and odors emitted, for example, during soldering, tinning, and similar operations, accompanied by strong heating of various substances, are captured by the DinCarb V M5 carbon filter, which is always installed as the final stage of cleaning.
To monitor the condition of the filter elements and their timely replacement, differential pressure gauges are installed on the door of each chamber.